Making jewelry is no longer a caste occupation in the Hindu social order as non-swarnakar are also finding a place in the craft. Counted in the informal sector the jewelry karigars are subjected to the crudest form of exploitation which leads to their alienation in the workplace. The elements of estrangement pervade their family and social life.
The everyday working lives of the karigars are like the playback singers behind beautiful actresses. A lot of hard work is ignored in the aura of gold jewelry. In this article, we pay our tributes to this great Indian Karigar! This article talks about the ‘behind the scene’ reality of the everyday working life of the karigars, their struggles, and sufferings, who work hard to create a beautiful world of art and fashion and fantasy in exchange for the bare minimum that is required for their survival.
It focuses on the daily routine of the karigars who spend a large part of their life in workshops for making jewelry. We will showcase the fantastic designs and techniques used by these Karigars to Indian jewelry designers and hobbyists. And hope to learn along with the Karigars while we pass on the tips and techniques to the readers.
The Jewelry Karigars Way
The great Indian jewelry Karigars have been creating rich & traditional beautiful jewelry for generations. They have been associated with the kings and queens once upon a time when they made royal jewelry. They have been successfully passing on the art to their heir and hence holding on to the traditional craftsmanship. Over the years, the art has modified itself to suit the designs and techniques as per the new era of jewelry. The Karigars now work with Indian jewelry designers, creating rich trendy collections.
India is known for its jewelry craftsmanship, and the artisans of this industry can trace their ancestry back to a long line of skilled professionals. These individuals are called Jewelry Karigars, and they play a vital role in the production of exquisite jewelry pieces for consumers around the world.
The process of crafting ornate jewelry has been passed down through generations, with each Jewelry Karigar learning the delicate art from their predecessors. The skill required to create such beautiful pieces is immense, with workmanship that often involves intricate detail and complex designs. India’s Jewelry Karigars combine traditional methods with contemporary techniques while using precious metals and stones to create stunning heirloom-quality jewelry collections.
Today, there are thousands of Jewelry Karigars throughout India who use their expertise to produce magnificent pieces for local and international markets. Most of these Karigars are involved in Microsetting, Wax Setting, Diamond Polishing and other artisan roles. Some of these karigars are good at Silver Idol Designs, Polishing and Smithing.
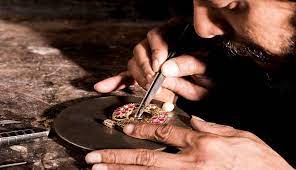
Types of Karigars
Making a single item of jewelry involves four kinds of specialist karigars, namely, melting wala, sona/rupa karigar, and polishing and shining wala. The melting wala’s work is to melt the gold bars.
Their work is to use this gold bar to make wires and smaller sheets of standard size by hammering or using machines. Then the sona/rupa karigars take up the gold wire from Patrawala for creating designs, molding the micro parts of an ornament, and soldering various parts of the design by heating it to form single finished jewelry products. They also give the finishing touches (glowing) to the gold jewelry.
The karigars, who work in the shops of the traditional swarnakars, play a crucial part in making jewelry. They also have their own workshops where they take an order from the local jewelry sellers who do not have any karigar of their own. They are the actual goldsmiths or Sona/Rupa Karigars. In the last category of the karigars, the polishing and shining walas, finally put a shine on the jewelry using indigenous techniques.
The process of jewelry making thus follows a standard division of labors among the specialist karigars, who work in harmony, although they are placed in a hierarchy in terms of payment and status. Several karigars who fall under the category patra wala and diewala say a common word related to their work.
Life of Jewelry Karigars
Karigars are an important part of the jewelry industry. Their art and skills transform the raw gold metal into fashionable gold jewelry which is adorned by both women and men; thus, they are the real goldsmiths. Their daily life consists of activities at work and family. The day-to-day activities of the karigars do not merely alienate them from the products they produce, but also from the working activities, which ultimately bring vulnerability in their family life as well.
They generally place themselves under the category of Vaishya caste (trader and merchants) in the Hindu caste hierarchy. The daily life of the karigars includes various responsibilities which are required to run the workshop. A jewelry workshop is a place or a system where a group of karigars is inter-dependently related to each other for making gold jewelry.
Health effects – Free movement of air inside the workshop is restricted in the absence of windows and ceiling fans. The working environment becomes intolerable due to rising heat, irritating smoke, and the smell of the chemical used for melting gold. For cooling down the temperature inside the workshop they use a table fan. While the work is on, the karigars are not allowed to use fans as it interferes with the process of making jewelry.
Inadequate ventilation and polluted air inside the workshop stress the karigars and cause fatigue and drowsiness. The karigars are made to inhale toxic particles day after day, thus inviting irreversible ailments. In general terms, this can be termed occupational hazards, but from the perspective of the karigars, it is a taken-for-granted realm of routine.
Indian Karigars Craftsmanship
India is recognized as the world’s biggest and best diamond and gem-cutting center. The country’s prowess is unsurpassed not just in gem-cutting, but also in creating exceptional jewelry – be it handmade or machine-made. Indian manufacturers have some of the most technologically advanced set-ups to create the finest of designer collections. Sadly, the industry has not done enough to promote its skills and strengths worldwide.
To gain global supremacy in the field of jewelry, the industry needs to introspect on factors such as design, the legacy of artistry, the welfare of artisans, and strong branding narratives, which together can empower the Make In India brand.
Experts suggest we move up the value chain by selling narratives woven around our precious heritage of jewelry-making crafts. They also hammer home the point that collectively we need to stop selling jewelry as a commodity, arguing that by charging a smaller premium we aren’t doing justice to artisans. Have we done enough to raise our global standing in jewelry-making?
We spoke to industry experts who shared their views on how India can further use its ability to achieve global status with luxury jewelry and narrow the gap between being perceived as a low-cost manufacturing center versus the rightful, spiritual home for high-quality jewelry.
Gem Cutting Skills
India’s jewelry-making and gem-cutting skills date back several centuries, and our industry is the torchbearer of these ancient crafts and rich heritage. Master craftsmen and skilled artisans have always been the backbone of this sector, who have handed down skills from one generation to the next to create pieces that are unparalleled in beauty and intricacy.
Today, India’s jewelry manufacturers cater to several international brands, and their artistry is not just restricted to making handcrafted jewelry. India-made jewelry fills showrooms around the world (last year we exported gems and jewelry worth nearly $36 billion), so what steps can the industry take to generate more awareness about our manufacturing strengths?
Why Indian Karigars are preferred?
There are only very few handful of jewelry retail brands that have made a mark internationally from India. India is not the first name that comes to mind when one thinks of designer jewelry. It has the tremendous potential to be counted as one of the luxury jewelry-makers of the world. Sadly India has not been able to leverage its prolific history of fine jewelry craftsmanship.
It’s not as though individual designers and manufacturers are not doing enough – they are attaining global recognition by creating a variety of contemporary and handcrafted lines. But there’s a huge scope in boosting Indian exports and becoming global leaders in all aspects of jewelry making — especially handcrafted jewels.
One needs to share and publicize stories of India’s skills in gem-cutting and jewelry making. India has leveraged her expertise in the gem-cutting segment at the global level. But perhaps design and quality and messaging about India such as jewelry, aesthetics, hand craftsmanship, designs, etc. are the most important factors to consider.
Enameling Works of Karigars
India is known for its fine enameling work – be it Benarasi or Jaipur meena work. Also the detailed filigree and naqashi work. And the magnificent temple and jadtar jewelry; the glass and gold fusion depicted in Thewa; bidri and dokra jewelry and the list is endless. So, weaving tales around artisans and their artistry is an important step in promoting Made In India.
Also, the collective resolve to recognize, retain and empower our supremely talented artisans will help add value to the home-grown ‘gurukuls’ that have been passing on the knowledge of jewelry crafts from one generation to the next for centuries.
In fact, our Karigars have traditionally been great designers — perhaps it is time to leverage that and draw our design talent from among our Karigars. We need to standardize the jewelry designs, sell the story of India, and revive hand-craftsmanship that itself is a big selling point – as people are looking at the sustainable model nowadays. Machine-made has its own place, but the value-add lies only in hand craftsmanship and we are totally ignoring this.
Future of Gems and Jewelry Craft Skills
In the future, the unique gems and jewelry craft skills of Indian Karigars needs to be nurtured and protected. This can provide both a critical comparative advantage and a scaffold to build global brands and migrate up value chains. It is critical therefore to enhance the economic viability, social respect of artisans, and their equitable integration into value chains. Sustainability is the future, which in this case integrates the survival of crafts with economic and career prospects, technology, and environmentally sound practices.
Today the core ideas of luxury are undergoing an extraordinary transformation. We inhabit a world in a world where consumers are increasingly demanding that the products they consume are multi-dimensional, tech-enabled, and imbued with social innovation and responsibility. We cannot continue to operate strategies based on definitions and practices of the last century if we want to evolve paradigms for our future in this one.
To understand and leverage our strengths to achieve synonyms with luxury jewelry, we have to understand what that term means to the consumers of tomorrow. We have to protect our craft and artisanal base, attract the best talent, increase education and awareness, and most of all, be willing to invest both capital and will for the same.
Skill Set of Jewelry Karigars
- Examine gems during processing to ensure accuracy of angles and positions of cuts or bores. You can do this using magnifying glasses, loupes, or shadowgraphs.
- Assign polish, symmetry, and clarity grades to stones, according to established grading systems.
- Estimate the wholesale and retail value of gems, following pricing guides, market fluctuations, and other relevant economic factors.
- Examine gem surfaces and internal structures, using polariscopes, refractometers, microscopes, and other optical instruments. In order to differentiate between stones, identify rare specimens, or to detect flaws, defects, or peculiarities affecting gem values.
- Identify and document stones’ clarity characteristics, using plot diagrams.
Soft Skills Needed
- Practical application to produce a piece that is desirable in the marketplace
- Practical ability to work with tools and materials, such as metals and gemstones
- Dexterity, attention to detail, and good hand-eye coordination
- Organisation and time-management skills and the ability to work to deadlines
- Commercial awareness and the confidence and temperament to be successful in the business world
- Ability to market yourself and your work
- Commitment to and passion for your work.
- Examine gems during processing to ensure accuracy of angles and positions of cuts or bores. It can be done using magnifying glasses, loupes, or shadowgraphs.
- Assign polish, symmetry, and clarity grades to stones, according to established grading systems.
- Estimate the wholesale and retail value of gems, following pricing guides, market fluctuations, and other relevant economic factors.
- Examine gem surfaces and internal structures, using polariscopes, refractometers, microscopes, and other optical instruments. This is to differentiate between stones, identify rare specimens, or to detect flaws, defects, or peculiarities affecting gem values.
- Identify and document stones’ clarity characteristics, using plot diagrams.
- Advise customers and others on the best use of gems to create attractive jewelry items.
- Examine diamonds or gems to ascertain the shape, cut, and width of cut stones. Also to select the cuts that will result in the biggest, best quality stones.
- Immerse stones in prescribed chemical solutions to determine specific gravities and key properties of gemstones or substitutes.
- Hold stones, gems, dies, or styluses against rotating plates, wheels, saws, or slitters. This is to cut, shape, slit, grind, or polish them.
Rough Diamond Polishing
- Sort rough diamonds into categories based on shape, size, color, and quality.
- Secure gems or diamonds in holders, chucks, dops, lapidary sticks, or blocks for cutting, polishing, grinding, drilling, or shaping.
- Locate and mark drilling or cutting positions on stones or dies, using diamond chips and power hand tools.
- Place stones in clamps on polishing machines and polish facets of stones. Using felt-covered or canvas-covered polishing wheels and polishing compounds such as tripoli and rouge.
- Lap girdles on rough diamonds, using diamond girdling lathes.
- Measure sizes of stones’ bore holes and cuts to ensure adherence to specifications, using precision measuring instruments.
- Select shaping wheels for tasks, and mix and apply abrasives, bort, or polishing compounds.
- Split gems along pre-marked lines to remove imperfections, using blades and jewelers’ hammers.
- Regulate the speed of revolutions and reciprocating actions of drilling mechanisms.
- Replace, true, and sharpen blades, drills, and plates.
- Secure stones in metal mountings, using solder.
- Dismantle lapping, boring, cutting, polishing, and shaping equipment and machinery to clean and lubricate it.
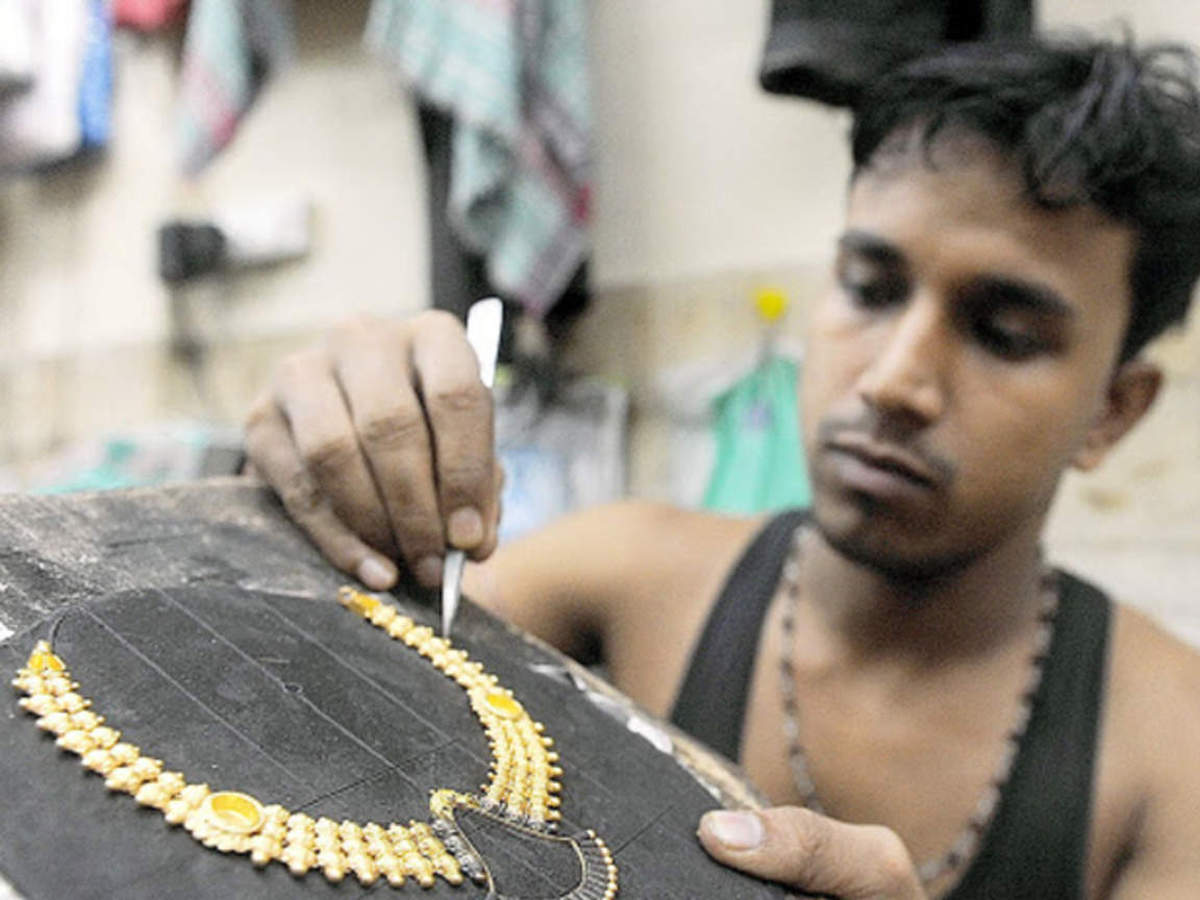
Detailed Work Activities of Jewelry Karigars
- Examine the physical characteristics of gemstones or precious metals.
- Evaluate the quality of materials or products. See more occupations related to this activity.
- Operate grinding equipment.
- Maneuver workpieces in equipment during production.
- Sort materials or products for processing, storing, shipping, or grading.
- Mount materials or workpieces onto production equipment.
- Record operational or production data.
- Advise others on ways to improve processes or products.
- Draw guide lines or markings on materials or workpieces using patterns or other references.
- Operate cutting equipment.
- Polish materials, workpieces, or finished products.
- Measure dimensions of completed products or workpieces to verify conformance to specifications.
- Apply solutions to production equipment.
- Mix substances to create chemical solutions.
- Select production equipment according to product specifications.
- Cut industrial materials in preparation for fabrication or processing.
- Drill holes in parts, equipment, or materials. See more occupations related to this activity.
- Sharpen cutting or grinding tools.
- Replace worn equipment components.
- Solder parts or workpieces.
- Disassemble equipment for maintenance or repair.
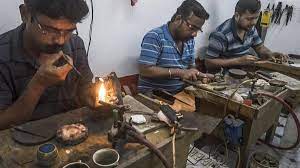
Jewelry Karigars Jobs
List of the frequently hired Jewelry Karigars Jobs
- Jewelry Designer
- Jewelry Maker
- Goldsmith
- Gemstone Setter
- Engraver
- Polisher
- Metalworker
- CAD/CAM Technician
- Stone Cutter
- Jewelry Repair Technician
Final Thoughts
In conclusion, it is clear that India is a great source for jewelry karigars. The artisans are highly skilled and experienced. They can also provide custom-made pieces of jewelry at very reasonable prices. The use of traditional techniques and craftsmanship makes Indian jewelry karigars a great choice for investing in timeless pieces. With the increase of Automation, karigars are upskilling their talent. Many karigars are moving from 2D Hand Made Sketching and Polishing to CAD Design and other automation tools. Are you looking to hire Jewelry Karigars? Try using Mintly to find the best talent in the Industry.